Device for aeration control: Control of aeration systems in WWTP
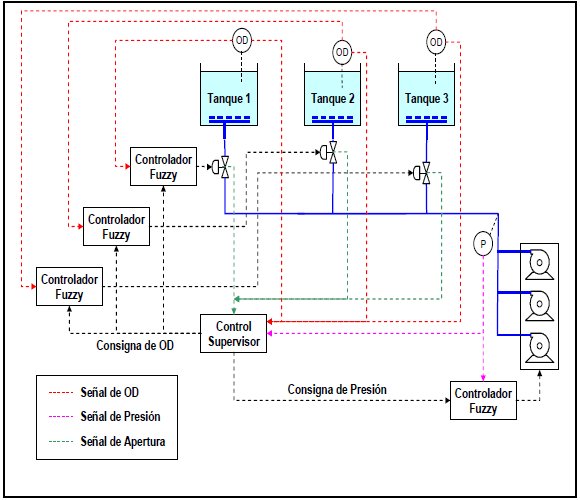
Description
Characteristics
Images
Description
The concentration of dissolved oxygen in activated sludge processes is considered as one of the most important control parameters in a WWTP. A low dissolved oxygen concentration affects the growth of the microorganisms that can cause the appearance of filamentous bacteria while a high concentration of oxygen supposes an important energy expenditure and negatively affects the process of denitrification.
It should be noted that the energy cost of aeration can account for more than 50% of the total energy cost of the treatment plant. For economic reasons as well as for reasons of stability of the process it is convenient to maintain a suitable dissolved oxygen concentration.
The CALAGUA research group has dedicated a great effort to the development of various control algorithms to optimize energy consumption and improve the stability of the biological processes in a WWTP. Regarding the control of the aeration system, the CALAGUA group has developed a control system based on fuzzy logic, which allows optimizing the overall operation of the aeration system in any plant that has aeration by diffusers and blowers.
Characteristics
The control system developed is based on fuzzy logic and establishes independent control loops for the dissolved oxygen in each aerobic zone of the biological reactor and for the discharge pressure of the blowers. By aerobic zone is meant that a reactor or part of a reactor equipped with an oxygen meter, one or more independent diffuser grids and a control valve that allows to regulate the airflow supplied by said grids. The concentration of dissolved oxygen in each of the aerobic zones is maintained at the setpoint by modifying the opening of the corresponding control valve, while the air discharge pressure can be controlled by modifying the rotational speed of the blowers by acting on the corresponding frequency inverter. This offers the possibility to aerate all the aerobic zones with a single set of blowers and to maintain different concentrations of oxygen in each of the zones. The movement of one valve does not affect the rest of the system because the control system maintains the pressure in the setpoint.
The control loops that modify the valve opening and the rotational speed of the blowers are based on fuzzy logic. The setpoint signals of these control loops are determined by a supervisory control algorithm. The supervisory control system is established at all times as the pressure controller’s setpoint the minimum value necessary for the correct operation of the system, thus reducing energy consumption. Said minimum value is the one that allows to maintain the concentrations of dissolved oxygen in the desired value, and one of the control valves open to 100%.
The figure shows the flow diagram of the proposed control system applied to the aeration of three tanks with a single group of blowers. Each oxygen sensor feeds an independent control loop that acts on the corresponding control valve. On the other hand, the pressure feeds the control loop which acts on the rotational speed of the blowers. From the information of the dissolved oxygen concentrations and the opening of the valves and the pressure, the supervisor control establishes the setpoints of all the control loops. The value of the pressure setpoint is modified to always keep one of the valves fully open.
The operation of the aeration system in these optimum operating conditions allows for considerable energy saving due to the maintenance of the valves to their maximum degree of opening, and minimizes the losses of load in the aeration system.
This control system has been implemented, among others in the Algemesí, Denia-Ondara-Pedreguer, Ontinyent-Agullent, Almassora, Gandía-La Safor, Castellón and Carraixet WWTPs, obtaining important energy saving results. As an example, in the WWTP of Algemesí, the energy consumption of the aeration system was been reduced by more than 40% compared to the situation before the implementation of the developed system.